Gear Grinding Case Study Gaining Efficiency to Meet Customer Demands
Challenge:
This customer was looking to improve the overall efficiency of their grinding operations to overcome issues they were having meeting customer order deadlines. They consistently had a backlog at their grinding machines causing them to miss customer order deadlines and were at risk of losing key customers.
Solution:
The Weiler Industrial Grinding Team designed a wheel utilizing a custom blend of high performance ceramic grain with microcrystalline grain to both increase metal removal rate and improve form retention. This grain combination paired with Weiler’s proprietary vitrified bond technology resulted in a grinding wheel that alleviated this customer's grinding backlog.
Result:
Weiler’s Custom Gear Grinding Wheel allowed this customer to increase overall grinding efficiency and meet their customers’ demands. The Weiler team utilized the Weiler Process Solutions Tool and presented the following improvements:
- MATERIAL REMOVAL RATE 43% INCREASE
- FORM RETENTION 51% REDUCTION IN DRESSING
- CYCLE TIME 44% REDUCTION
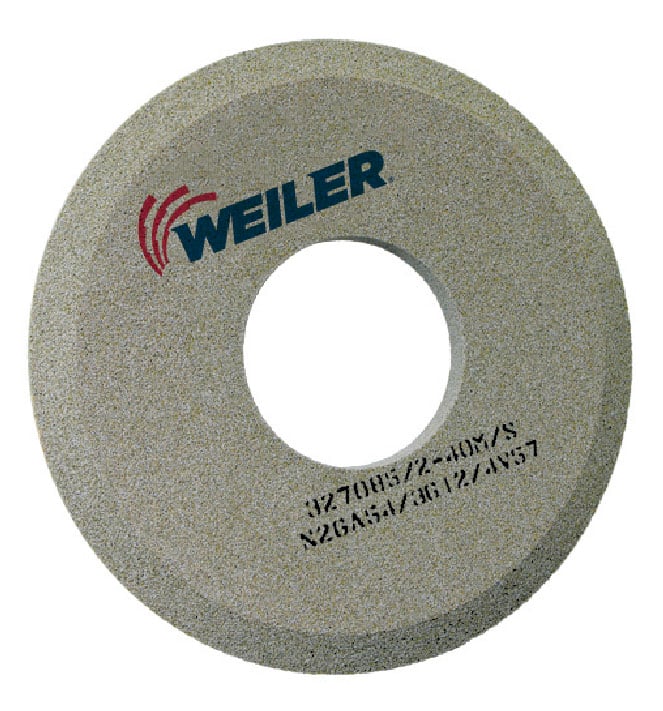
43% Increase
51% Reduction in Dressing
44% Reduction
Contact Us For Next Steps:
Call Weiler's Customer Experience Team at 800.835.9999. Our Application Engineers are available 8:30am to 5pm EST, Monday - Friday.
Or use our Application Assistance Form below and one of our Engineers will recommend a process or the best product to solve your problem at the lowest possible end-use cost.