Deburring
Deburring Solutions: Your Guide to Precision and Efficiency
In the world of manufacturing and fabrication, precision is everything. Deburring, the process of removing sharp edges, burrs, and imperfections from machined or fabricated parts, plays a pivotal role in achieving that precision. It ensures that components meet stringent quality standards while enhancing their functionality and longevity.
Beyond aesthetics, deburring is critical for product quality, safety, and efficiency. Improperly deburred parts can lead to performance issues, compromised safety, or premature wear, impacting both the end product and your bottom line. From metal to composites and beyond, deburring is the key to achieving required finishes and safer operations.
At Weiler Abrasives, we understand the importance of reliable deburring processes. As a leader in innovative surface conditioning solutions, we are dedicated to helping you achieve precision and efficiency in every project. With cutting-edge products and industry expertise, Weiler is your trusted partner for deburring applications that drive success.
Our guide walks you through the essentials of deburring, from understanding the types of burrs to exploring the best tools for achieving precision. Whether tackling basic tasks or complex industrial applications, you'll learn practical tips and actionable strategies to optimize deburring processes for superior quality.
Deburring Basics 101
Burrs are unwanted raised edges or small pieces of material that remain attached to a workpiece after machining operations such as grinding, drilling, milling, engraving, or turning. They can compromise the functionality, safety, and aesthetics of machined parts, making deburring—a process to remove these imperfections—an essential step in manufacturing. Let’s explore the main types of burrs, the materials where they are most frequently encountered, and the critical role of deburring.
Primary Types of Burrs
- Rollover Burrs: The most common type, rollover burrs occur when material bends over the edge during cutting, resulting in a curled protrusion. This typically happens at the exit side of a cut where the tool pushes through the material.
- Poisson Burrs: These form when compressive forces cause the material to bulge outward or sideways during machining. Named after the Poisson effect, they often appear as lateral protrusions on the workpiece.
- Breakout Burrs: Also known as cutoff burrs, breakout burrs occur when a part is separated from the material before the cut is finished, leading to a rough, fractured edge.
Materials Prone to Burr Formation
Burr formation is common across various materials, each presenting unique challenges:
- Steel: Known for its hardness, steel can develop sharp burrs that may compromise assembly precision and increase wear on mating components.
- Aluminum: This lightweight, ductile metal is prone to burrs due to its softness, which can affect surface finish and dimensional accuracy.
- Exotic Alloys: Materials like titanium and Inconel, used in high-performance applications, often generate tough burrs that are difficult to remove, necessitating specialized deburring techniques.
The Importance of Deburring
- Enhanced Functionality
Burrs can interfere with the operation of mechanical systems by disrupting the precise assembly or movement of components. For example, burrs on gears can lead to misalignment, increased friction, and accelerated wear, resulting in premature failure. Similarly, in hydraulic systems, burr particles can break off and contaminate the fluid, compromising seals and causing malfunctions. Removing burrs ensures parts fit and function seamlessly, reducing the risk of operational issues and enhancing overall system performance.
- Improved Safety
Sharp edges or protrusions caused by burrs are a serious safety concern for both workers and end-users. Handling burr-laden components can result in cuts, abrasions, or other injuries, especially for assembly-line operators or technicians. For consumers, sharp edges left on products like tools or medical devices can lead to harm during use. By eliminating burrs, manufacturers can improve workplace safety, protect end-users, and ensure compliance with safety standards.
- Extended Component Life
Burrs create stress concentrations in materials, serving as weak points that are more likely to crack or fail under pressure. Additionally, burrs can trap moisture, dirt, or other contaminants, increasing the risk of corrosion and wear. In high-stress applications, such as aerospace or automotive components, these imperfections can compromise structural integrity and reliability. Removing burrs reduces these vulnerabilities, ensuring parts perform consistently and have a longer lifespan.
- Optimized Efficiency
In modern manufacturing processes, especially those relying on automation and precision, burrs can cause significant inefficiencies. Robotic assembly systems may struggle to handle parts with irregular or jagged edges, leading to slowdowns or errors in production. Additionally, burrs can disrupt the precision tolerances required in CNC machining and other high-tech processes. By incorporating deburring into production workflows, manufacturers can maintain precision, reduce errors, and improve the overall efficiency of their operations.
- Improved Aesthetic Quality
The appearance of a finished product plays a significant role in customer satisfaction, especially in consumer-facing industries. Burrs and rough edges detract from the visual appeal and perceived quality of a product, potentially impacting sales and brand reputation. Deburring results in a smooth, brushed finish that enhances the product’s aesthetics, delivering a professional finish that meets customer expectations and supports brand credibility.
- Regulatory and Industry Compliance
Many industries, such as aerospace, automotive, and medical devices, have strict standards requiring deburring as part of the production process. Non-compliance with these standards can result in penalties, product recalls, or reputational damage. For example, aerospace parts must meet stringent safety requirements, and even minor defects can lead to catastrophic failures. Manufacturers that adhere to deburring protocols ensure compliance with industry regulations protecting their reputation and market position.
- Cost Savings
While deburring may require additional time and resources, it significantly reduces long-term costs. Burrs can lead to expensive issues, such as the need to repair or replace damaged parts, downtime caused by equipment malfunctions, or product returns due to poor quality. Manufacturers can prevent these problems by investing in deburring processes. A proactive approach not only saves money but also boosts productivity and customer satisfaction.
Industries and Applications for Deburring
Deburring is a critical process across a wide range of industries, ensuring parts meet performance, safety, and aesthetic standards. Below, we explore how deburring applies to key industries and provide practical examples of its importance.
- Metal Fabrication and Pipeline: In the metal fabrication and pipeline industry, deburring is essential for ensuring clean edges and smooth surfaces on machined or cut metal components. Removing burrs improves weld quality and reduces the risk of corrosion or structural failure in pipelines. Preparing metal sheets for assembly or ensuring precision in flanges and pipe joints are typical applications of deburring in this sector.
- Automotive and Aerospace: Precision and reliability are paramount in automotive and aerospace manufacturing. Deburring results in smooth, burr-free components, which is crucial for maintaining performance and safety standards. Deburring wheel hubs prevents premature wear, while smoothing turbine blades in aerospace enhances aerodynamic efficiency and reduces vibration.
- MRO (Maintenance, Repair, and Operations): In MRO activities, maintaining and repairing critical equipment often involves reconditioning parts such as gears, shafts, and bearings. Burr removal helps these components meet operational specifications, extending the life of machinery and preventing uneven wear caused by residual material.
- High-Volume Production: Manufacturers involved in high-volume production rely on in-machine deburring to streamline operations and maintain consistency. This process integrates deburring directly into CNC machining centers or other automated systems, eliminating the need for manual intervention and reducing production bottlenecks.
- Construction: Construction projects rely on durable and precisely machined components. Removing burrs from steel reinforcements, brackets, or other hardware not only enhances structural integrity but also ensures safety during handling and installation. The deburring step contributes to higher-quality construction assemblies.
- Energy and Power Generation: High stress and demanding conditions in the energy sector make deburring a vital step for ensuring equipment reliability and efficiency. Smooth edges on wind turbine components or heat exchangers help improve performance and extend their operational lifespan.
- Shipbuilding and Marine: In shipbuilding, ensuring the longevity and safety of marine structures and vessels often hinges on deburring. Removing burrs from welded joints or metal plates minimizes corrosion risks and leaves water-tight integrity. Enhanced hydrodynamics and fuel efficiency are achieved by refining propeller blades.
- Railway Maintenance: Railway maintenance depends on deburring to maintain the integrity and performance of rail components. Cleaning up weld seams on rolling stock or smoothing rail tracks ensures durability and safe operation, helping to prevent potential issues caused by defects.
- Food and Pharmaceutical: Hygiene and compliance are crucial in the food and pharmaceutical industries. Burr-free surfaces on machinery like mixers and conveyors help maintain cleanliness and reduce contamination risks. Ensuring stainless steel processing equipment meets stringent sanitary standards is a common application of deburring in these industries.
Challenges in Deburring Operations
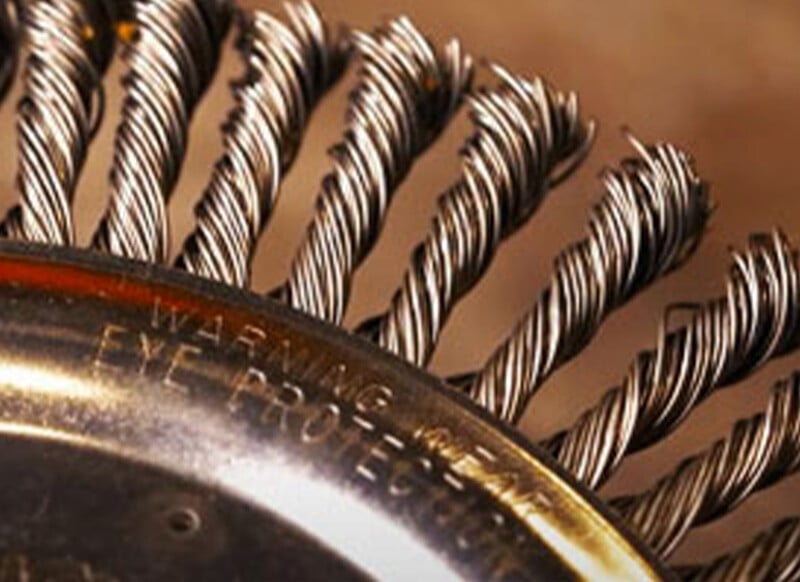
Achieving Precision Without Damaging Parts
One of the primary challenges in deburring is the need to remove unwanted material without harming the integrity of the part. Precision is paramount, especially for high-tolerance applications in industries such as aerospace, automotive, and medical devices. Over-deburring can lead to dimensional inaccuracies, while under-deburring may leave burrs that compromise functionality or safety.
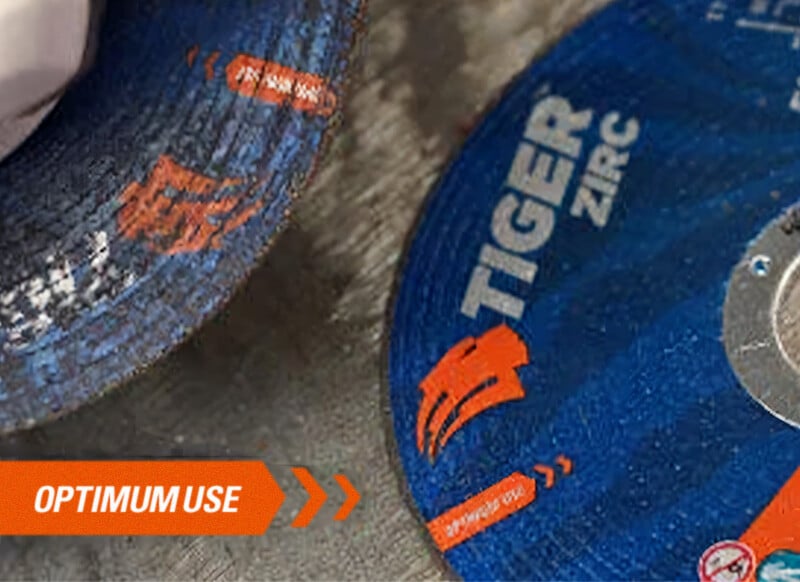
Consistency in Removing Burrs from Irregular or Complex Shapes
Irregular or complex part geometries, such as internal holes, sharp corners, or intricate designs, present a unique challenge. Ensuring consistent deburring across all surfaces can be time-consuming and labor-intensive. Traditional methods may struggle to reach these areas effectively, leading to variability in quality.
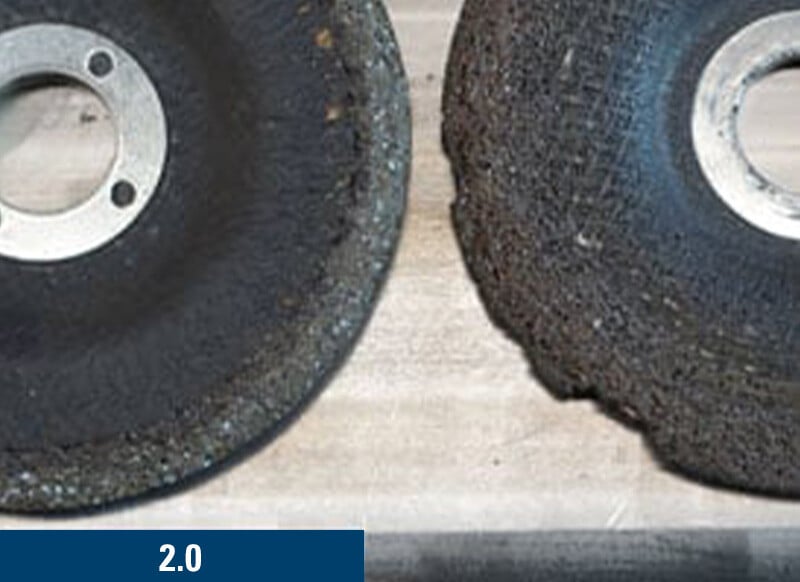
Tool Wear and Replacement Costs
Due to the abrasive nature of the process, deburring tools are subject to significant wear. Frequent tool replacements not only increase operational costs but also result in downtime. Finding tools that balance durability and performance is essential for cost-effective operations.
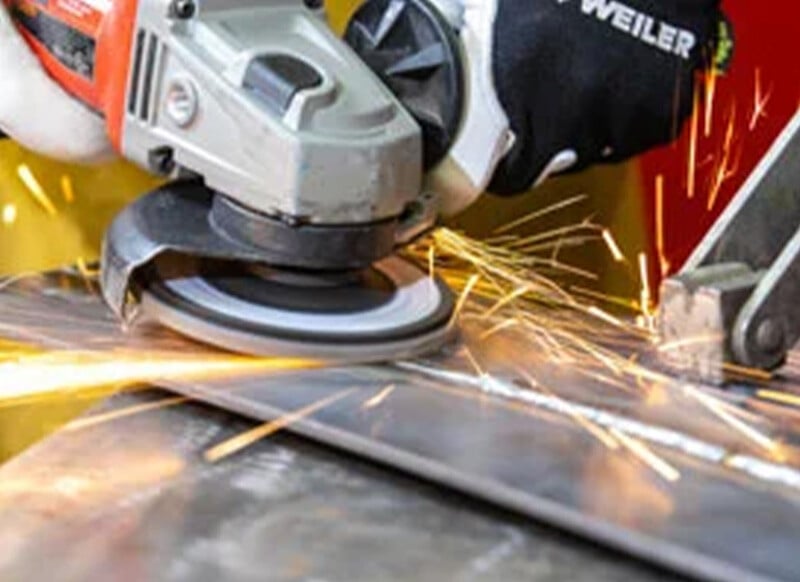
Operator Fatigue and Safety
Manual deburring operations can be physically demanding, requiring operators to maintain precision and focus over extended periods. Such a process can lead to fatigue, which not only affects productivity but also increases the risk of errors or accidents. Additionally, sharp burrs and flying debris pose safety hazards, emphasizing the need for ergonomic tools and proper protective equipment.
Addressing these challenges requires a combination of advanced tools, innovative technologies, and safety best practices tailored to the operation's specific needs.
Choosing the Right Deburring Tools
Selecting the ideal deburring tools for your application is crucial to achieving optimal results while maximizing efficiency and tool lifespan. Here are several factors to consider when choosing the right tools for deburring tasks.
Key Factors to Consider
Material Type and Thickness: The type of material being processed significantly impacts the choice of deburring tools. For softer materials like aluminum, tools with less abrasive power may be suitable to avoid damaging the surface. Harder materials, such as stainless steel or titanium, require tools with greater durability and cutting capability. Material thickness is equally important, as thicker materials may necessitate heavier-duty tools to effectively remove burrs.
Application Requirements: Understanding your application requirements is essential. Consider the following:
- Finish Quality: Some applications demand a smooth, polished finish, while others prioritize functionality over aesthetics. Select tools with appropriate abrasive properties to meet these needs.
- Speed and Efficiency: For high-volume operations, tools that can remove burrs quickly without compromising quality are vital. Conversely, precision tasks may benefit from tools designed for slower, more controlled operations.
Tool Compatibility with Manual and Automated Systems: Determine whether the deburring process will be performed manually or with automated equipment. Manual tools offer greater flexibility and are ideal for intricate or hard-to-reach areas. On the other hand, automated deburring systems are well-suited for high-volume production and consistent results. Ensure that your chosen tools are compatible with the systems in use, as mismatched tools can lead to inefficiencies or damage.
Industrial Deburring Tools Overview
Deburring tools designed for industrial applications come in a variety of designs, each tailored to specific production needs and material types:
Rotary Deburring Tools
Rotary tools, such as carbide burrs and flap wheels, are staples in industrial environments. Used with handheld or automated systems, they excel at removing burrs from complex or irregular surfaces and are available in a variety of grits and sizes for different applications.
Shop our extensive line of flapwheels
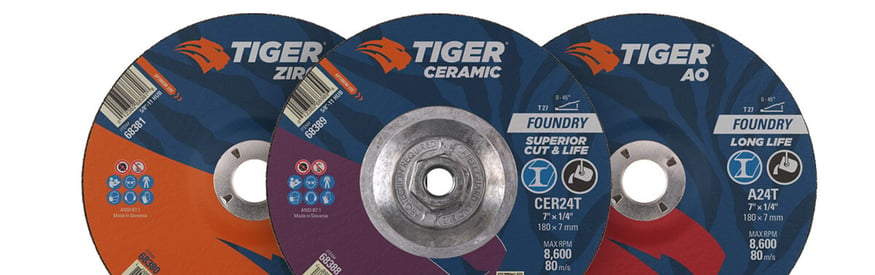
Abrasive Brushes
Industrial-grade abrasive brushes are used for precision finishing and deburring in both manual and automated systems. They’re effective for removing light burrs while achieving consistent finishes on metal, composites, and other materials.
Shop our extensive line of abrasive power brushes
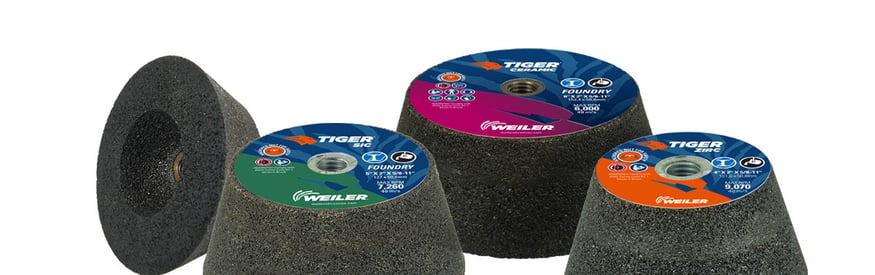
Deburring Wheels
Deburring wheels are highly durable and engineered for automated production lines. These tools are ideal for high-volume operations, offering consistent results across a range of material types and geometries.
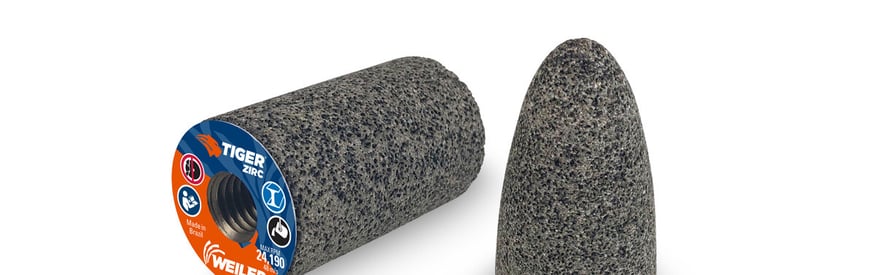
Tumbling Media Systems
For batch processing, industrial tumbling media systems provide a scalable solution to deburring. These systems can process hundreds of parts simultaneously, making them suitable for small components in large quantities.
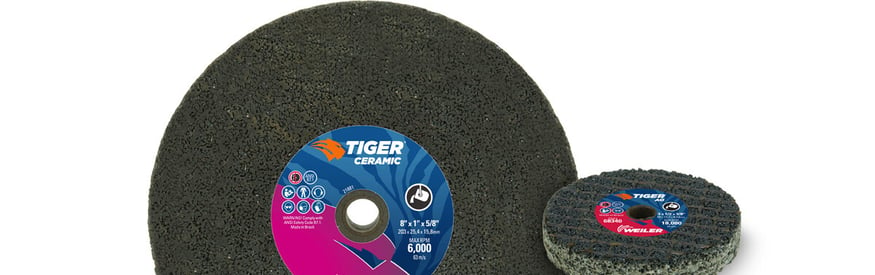
Precision Cutting Tools
For applications requiring extremely fine deburring, precision cutting tools such as specialized end mills or countersinks offer controlled material removal. These are often used in CNC machining setups.
Shop our extensive line of cutting wheels
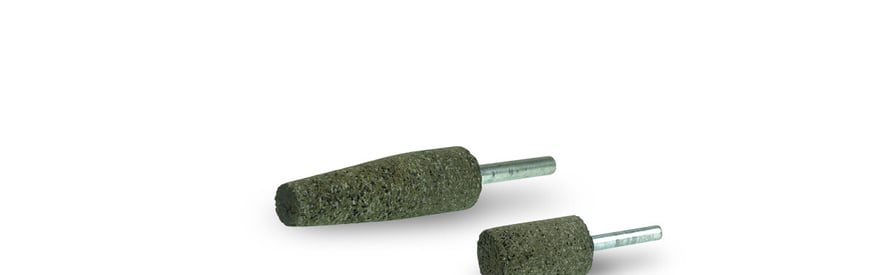
Best Practices for Effective Deburring
Safety Guidelines
Ensuring safety in deburring operations is paramount for protecting operators and maintaining a productive workplace.
- Importance of PPE (Personal Protective Equipment)
- Always wear appropriate PPE, including gloves to protect hands from sharp edges, goggles or safety glasses to shield eyes from debris, and hearing protection when using loud tools and equipment.
- Check PPE is in good condition and appropriate for the specific deburring application.
- Proper Handling and Storage of Deburring Tools
- Handle deburring tools with care to prevent accidental injuries.
- Store tools in designated areas to avoid damage and ensure they remain in optimal working condition.
- Inspect tools regularly for wear, damage, or defects that could compromise safety or performance.
- Machine Setup and Inspection Tips
- Before starting any deburring process, check that the machine is properly set up and calibrated for the specific material and tool being used.
- Inspect equipment for loose components, worn parts, or misalignments.
- Ensure all safety guards and emergency stop functions are operational.
Efficiency Tips
Maximizing the efficiency of deburring operations not only improves output but also extends the lifespan of tools and equipment. Consider the following best practices.
- Matching Tools to Applications for Optimal Performance
- Select deburring tools designed specifically for the material being processed and the desired finish.
- Utilize application-specific brushes, discs, or belts to achieve consistent results and avoid over-processing.
- Reducing Tool Wear and Maximizing Lifespan
- Follow manufacturer guidelines for tool usage, including recommended speeds and pressures.
- Rotate and replace tools as needed to maintain consistent performance and reduce strain on equipment.
- Use cooling or lubrication methods where appropriate to minimize heat buildup and prevent premature wear.
- Workflow Optimization to Minimize Downtime
- Organize workstations for easy access to tools and materials, reducing unnecessary movement.
- Implement regular maintenance schedules to keep equipment in peak condition.
- Train operators on efficient deburring techniques to maintain consistent quality and throughput.
Why Weiler for Deburring Solutions?
Innovation Driving Performance
Weiler takes a comprehensive approach to innovation, addressing both product development and operational challenges. The Weiler Process Solutions (WPS) program is a testament to this vision, providing customers with expert-driven strategies to enhance grinding processes, lower costs, and deliver superior results.
Quality That Delivers Results
With a focus on precision and reliability, Weiler employs advanced manufacturing processes and exhaustive testing to uphold the highest standards. Every grinding product is meticulously inspected to guarantee optimal safety and performance, enabling customers to achieve consistent results and streamline operations.
Technical Support: Expertise When You Need It
Customers benefit from technical support that covers more than just product selection, with a focus on application-specific guidance. Process optimization services conducted on-site enhance the efficiency and value of deburring operations. Operator training sessions provide expertise in effective techniques and safety standards. Documentation support ensures seamless performance across all teams and operational shifts.
- New innovations help you meet environmental standards and sustainability expectations
- World-class research, development, and manufacturing capabilities keep your business ahead of the competition
- Proprietary technologies and global access to abrasive deburring solutions provide flexibility and freedom to develop limitless solutions
- Stable supply and local inventory to keep your business running smoothly and reduce your inventory burden
- On-site technical support and education to keep your cutting process optimized and your people safe
- Engineered solutions tailored to your specific applications
Our Customers Experience Unparalleled Results
“I just don’t want to be a gear supplier. I want to be a partner. And I think Weiler has done a good job of doing that with Rave.”
Duis aute irure dolor in reprehenderit in voluptate velit esse cillum dolore eu fugiat nulla pariatur. Reprehenderit in voluptate velit esse cillum dolore eu fugiat nulla pariatur.
Duis aute irure dolor in reprehenderit in voluptate velit esse cillum dolore eu fugiat nulla pariatur. Reprehenderit in voluptate velit esse cillum dolore eu fugiat nulla pariatur.